With the benefit of government grant funding, The Evergreen State College (TESC) Clock Tower seismic improvements project combined the new technologies of Carbon Fiber Wrap and 3D Building Information Modeling to deliver success.
The Evergreen State College (TESC) Clock Tower was built in the early ’70s, and has become the icon of the campus and nearby community as the tallest, most visible thing for miles around. It has always been a central meeting place for students, and it’s even been rappelled by a few local notables. Two infamous for doing so were Washington State Governor Dan Evans and mountaineer Willi Unsoeld.
Like many of us who date from the early ’70s, it was still strong but starting to show its age! And although it didn’t sustain damage from the 2001 Nisqually earthquake, the seismic codes since it was constructed have changed a lot. The reinforced concrete structure was at risk of catastrophic failure during a significant seismic event. To help make the building safe for future generations of students, improvements were needed.
The College understood the safety issue and began a study of the Clock Tower in 2007. The project became the College’s number one hazard mitigation priority two years later. Using the 2007 study’s findings, they applied for a mitigation grant from FEMA. This required considerable finesse because no one lives or works in the Clock Tower, and aside from providing an exterior stair for the library, the tower’s aesthetic purpose is to conceal a ventilation shaft for the library. To demonstrate a risk to life and limb (according to the grant’s purpose), FEMA wanted to know the relative damage that would be caused if the tower fell in various directions. Falling into the campus’s main square was judged less dangerous than falling into the library. The College sorted through all of this, showed that the cost/benefit calculations worked, and received the grant.
As you likely know, grants come with strings attached. Seismic grants don’t pay for things unrelated to seismic issues. Also, should the final project cost come in higher than expected, the College may be on the hook to pay for the difference. In the state’s post-2008 financial situation, this was not a good option. This put a challenge on the design team to come up with a design that works within a budget that was prepared based on limited information early in the project’s life. We had to do three things:
- Upgrade the tower to current seismic code
- Do the upgrades for a price set three years earlier
- Leave the final appearance unchanged
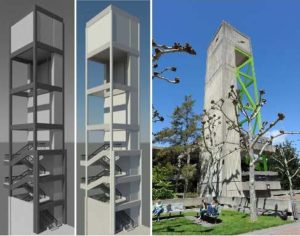
It is a good thing that engineers enjoy a challenge.
Reid Middleton did a formal study considering a variety of options. As part of this, Building Information Modeling (BIM) was used to create 3-D renderings of the various options, and how they would affect the building’s appearance. This work culminated in a presentation to the College Board. As they say, a picture is worth a thousand words. Renderings of the completed project helped decision-makers move past speculation to understanding.
The solution that was selected for achieving all three objectives was a carbon fiber wrap. This technique wraps existing concrete in a thin layer of carbon fiber fabric. Carbon fiber is the same material that is being used for Boeing’s new 787 (although the aerospace industry buys a higher grade). The building-grade carbon fiber is strong though. One square inch of it can support 140,000 pounds. That means that a fiber rope no bigger around than my wrist could lift one of those 787s. Carbon fiber wraps also have the advantage of being thin. A few layers on the outside of the building typically add less than ¼ inch. With a good coat of sand-rich paint, the final appearance isn’t very different.
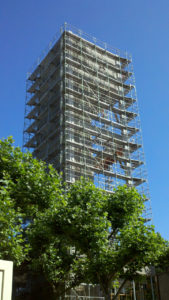
When combined with concrete, carbon fiber does a few things. First, it adds to the strength. The beams, columns, and walls were all strengthened. Second, it adds to the ductility. Ductility is a good engineering word that means the ability of a system to sustain movement, and potentially damage, without failing. At a basic level, concrete is a collection of rocks that are cemented together. When this assembly cracks in a severe earthquake, it can try to return to its roots as a collection of rocks and fall apart. A fiber wrap holds the assembly together. A great analogy is a sand bag. A sand bag is strong, because the bag is holding the sand together. This isn’t hard to apply either. It goes on in a manner similar to wallpaper, with higher quality-control standards.
All of this came together during construction. A mock-up was key to this effort. The contractor prepared a small portion of the tower with the intended finish and held a big meeting for stakeholders to look at it, refine the approach, and know their concerns were addressed.
The final product is improved safety and, in my opinion, improved appearance too. The appearance wasn’t changed much, but it regained a cleanness and crispness that the tower has lost over the years…like many of us from the early ’70s have.
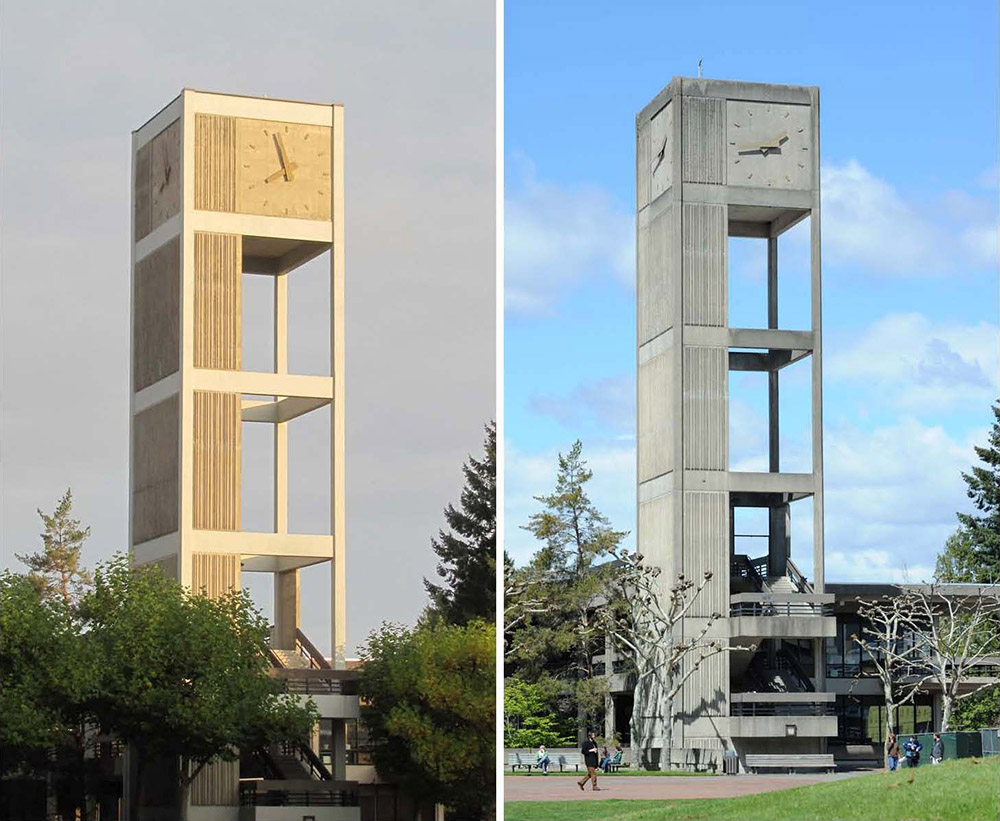